Many journalists pride themselves on their ability to make anyone talk—sometimes revealing secrets they wouldn’t even tell their spouses. I considered myself one of them. That is, until I met Ernest Simeoni
We arrived at his office in Nairobi’s Industrial Area at 8:45 a.m. for a 9:00 a.m. interview. We didn’t start rolling until 11:00 a.m. Why?
First, my cameraman faced a near-impossible task: setting up in a tiny, cluttered 4x2 meter office (probably smaller—it certainly felt like it). The space was packed with products, equipment, decorations, files, and what seemed like an archive of the entire Nilotic communities of East Africa. And yet, somehow, amid all that, there was still room for a hive of live, buzzing bees—yes, real bees—freely coming and going through an open window overlooking industrial go-downs and hopeful job seekers.
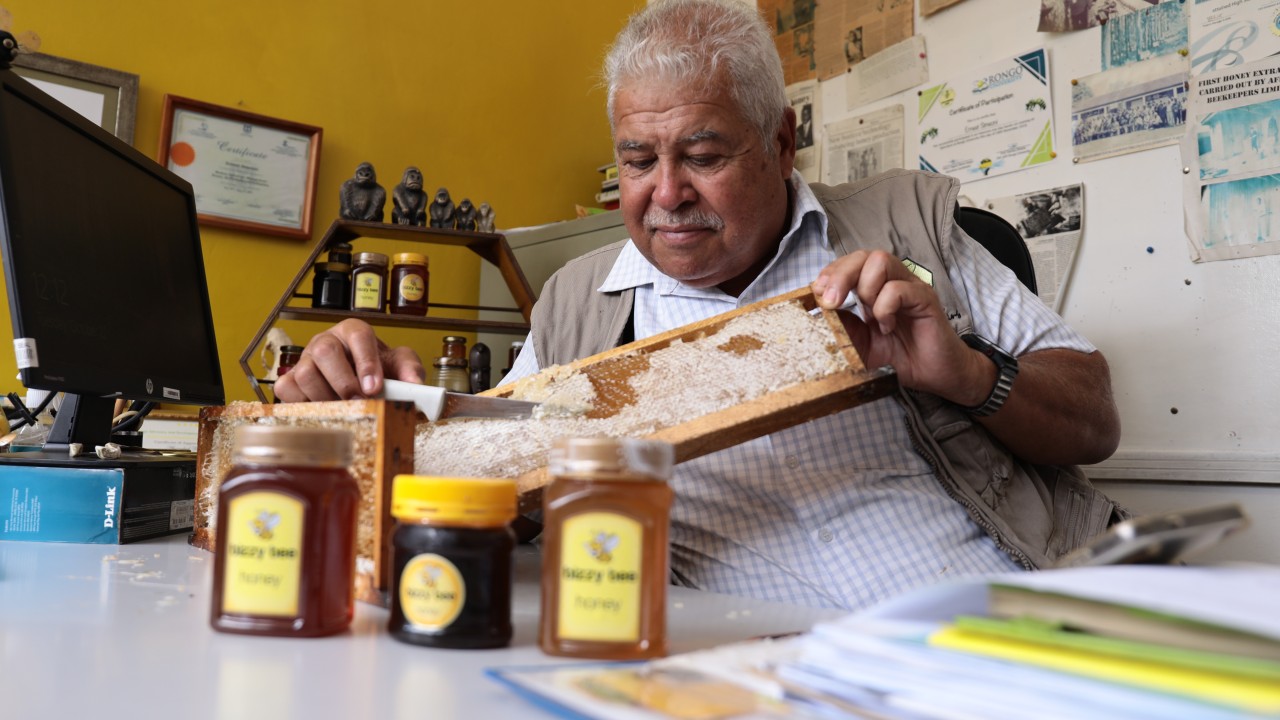
Ernest Simeoni, Director Africa Beekeepers LTD explains what happens when a honey comb is capped. Photo by @Duncan Lukoye
Second, I had to convince Ernest that I wasn’t just another journalist chasing a quick feel-good story. I was genuinely interested in beekeeping.
Ernest is the managing director of Africa Beekeepers Limited (ABL), a company that not only keeps and manages bees but also produces beekeeping equipment. With three decades in the industry, he knows beekeeping inside out. And if there’s one thing he’s certain about, it’s that the media rarely gets the story right.
"Beekeepers? We’re Professional Liars"“Beekeepers—we’re professional liars,” Ernest says with a chuckle. “People exaggerate everything—the number of hives they manage; the honey they produce. And why? Because industry players, especially equipment suppliers, sell a rosy narrative that attracts development organizations looking to fund sustainable livelihoods in the ASAL regions.”
And journalists? “They enable it,” he says. “They love the success stories but never dig into the challenges or the process.”
Ernest started ABL 30 years ago with a simple plan: buy honey in bulk from farmers, package it, and export it to the U.S. and Europe. Easy money.
Reality check? In three decades, he has exported a grand total of three tonnes—just one tonne per decade, you could say. Instead of a goldmine, beekeeping has become a full-time labour of love that has promised fortune but delivered mostly knowledge.
One of his biggest lessons? The success of beekeeping isn’t just about hives—it’s about thriving ecosystems and sustainable practices.
“I think we need to redefine beekeeping in this country,” he says. “What we have is honey hunting. Beekeeping is about managing bee colonies—no destruction, no killing of bees.”
Revolutionizing the Honey BusinessTo counter poor practices, Ernest and his team at ABL developed a structured system. They provide farmers with hives fitted with framed combs made from natural wax at their Industrial Area workshop. Farmers are trained to care for both the hives and the environment around them.
“This is a major quality control measure,” he says. “There’s a lot of honey adulteration. Sometimes, when you buy from farmers, you don’t even know what you’re getting.”
When the honey is ready, ABL picks up the frames, replaces them with empty ones, and transports the honey-filled combs to Nairobi for processing.
“We only buy honey that’s capped,” Ernest explains, holding up a perfectly sealed honeycomb. “When bees fill the comb, they seal it with wax after reducing the moisture to 18-19%. That’s how you know it’s ready—no fancy instruments needed.”
He scoffs at the term ‘refining honey’.
“Honey is refined by bees in the hive! All we do is extract it and put it in a bottle. That’s the value addition—taking it from here” (he points to the comb) “and putting it in here” (gesturing toward a jar).
Unlike conventional harvesting, ABL’s method preserves the comb during extraction. This, Ernest says, is critical.
“Some flowers produce nectar for only two or three weeks. If you destroy the combs, the bees waste time rebuilding instead of making honey. But if you return an intact comb, they get straight to work. That’s how you maximize production—you can even get two or three harvests a season if you're lucky.”
A Model for Sustainable BeekeepingThis approach has earned ABL a place in the Tana Greenheart Project, an initiative led by Nature Kenya that promotes sustainable livelihoods and conservation in the Tana Delta.
The delta’s rich biodiversity offers huge potential for high-quality honey production.
“Different flowers produce different colours and flavours of honey,” Ernest explains. “The international market is very particular about that. If you can get unique flavours, that’s what sells.”
The Biggest Lesson? Patience.Thirty years in, what has Ernest learned? “The biggest lesson? Patience.” He offers the same advice to farmers in the Tana Delta.
“Beekeeping isn’t a get-rich-quick scheme. If they’re patient, they’ll learn, produce consistently—both in quality and quantity—and do it sustainably.”
And with that, he picks up a honeycomb, tilts it toward the light, and smiles.
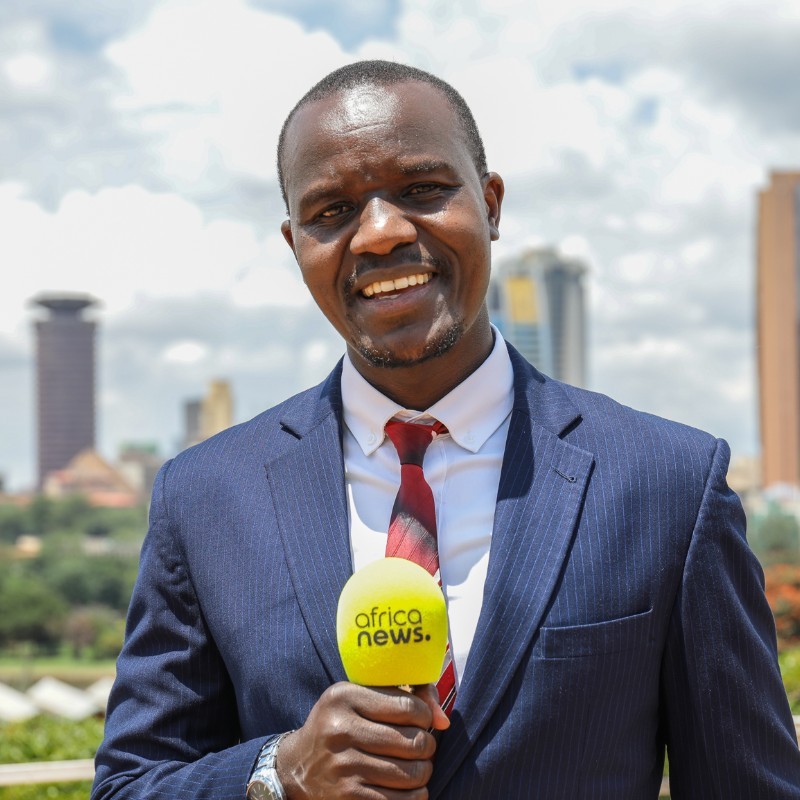
About the author:
David Owino is a journalist and is the Kenyan correspondent for Africa News.